Rittmeyer AG Case Study: 3% More Generated Power
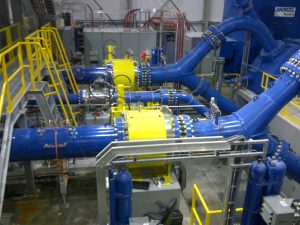
Optimizing turbine efficiency based on flow data
Rittmeyer made a case study in the US at the Stuyvesant Falls Hydroelectric Plant near Albany, N.Y. The results are highly interesting.
Stuyvesant Falls Hydroelectric Plant was built in 1899. It was purchased by Albany Engineering in 2008, modernized and placed back in to service in 2012.
The Stuyvesant Falls case showed tremendous advantages to knowing the true flow, even in a small hydro station. While not all plants will realize these dramatic results, in a fleet of hydro stations it’s likely that plant operations can be optimized overall and efficiency gains realized. Even an average of 1% improvement could lead to a rapid repayment of the investment and significant long term increases in net profits. Additional benefits could be realized in maintenance and CapEx management.
Flowmeter Considerations
This site is well-suited for a transit time flowmeter with a long straight run of penstock approximately 20 pipe diameters entering the powerhouse. Since this was an operating efficiency test, as opposed to a turbine performance test, relative flow uncertainty is more important than absolute uncertainty. Therefore, a lower cost Rittmeyer RISONIC modular transit time flowmeter with a pair of clamp-on transducers in a 1E1P single path arrangement was selected.
Flow Data Leads to a New Turbine Strategy
Flow tests were run in April 2016. A sequential unit deployment strategy had been utilized. It called for one unit to be run as needed up to the peak efficiency point. If more water was available, then the first unit was left at peak and the second unit was brought on as water allowed.
The new flow data showed that this strategy was not optimum. Due to the much lower efficiency at low flows, more power could be generated with a balanced unit approach. This new strategy calls for immediately backing the first unit down as the second unit is deployed so that both are running at equal output. Data from the previous 12 months of operation, which represent a fairly typical year, were used to analyze potential benefits of the new operating strategy. The results showed that an additional 1.3% of power could have been generated if the new unit deployment strategy had been employed. For various reasons, Unit 2 has always been used as the primary unit, making it the first to come up and the last to shut down. The new turbine data revealed a significant difference in turbine efficiency with Unit 1 having 2.3% greater efficiency, on average.
Total Generation Improvements
Using this data and the subsequent analyses, an estimated 2.7% more energy can be generated in a typical year by utilizing the new unit deployment strategy and making Unit 1 the primary. That number could be > 3.4% in a good water year.
Financial Results
A simplified financial analysis indicated that the flowmeter investments could be paid off in a matter of months. Since efficiency improvement transfer almost directly to the bottom line, that can translate to net profit improvement many times higher than the 2.7% additional revenue.
Conclusion
The Stuyvesant Falls case showed tremendous advantages to knowing the true flow, even in a small hydro station. While not all plants will realize these dramatic results, in a fleet of hydro stations it’s likely that plant operations can be optimized overall and efficiency gains realized. Even an average of 1% improvement could lead to a rapid repayment of the investment and significant long term increases in net profits. Additional benefits could be realized in maintenance and CapEx management.
For more information about Rittmeyer flowmeters, click here.
Established in 2000, Cascadia Instrumentation Inc. is a manufacturer’s representative and distributor of high-quality instrumentation products for the industrial and commercial sectors. We serve a wide range of industries, including Manufacturing, Water & Waste Treatment, Hydropower, District/Thermal Energy and Process industries including Pulp & Paper mills, Ore Processing and Chemical plants and Gas Processing. We have exclusive representation agreements with leading instrumentation manufacturers located in Canada, the USA, Switzerland and Germany.